
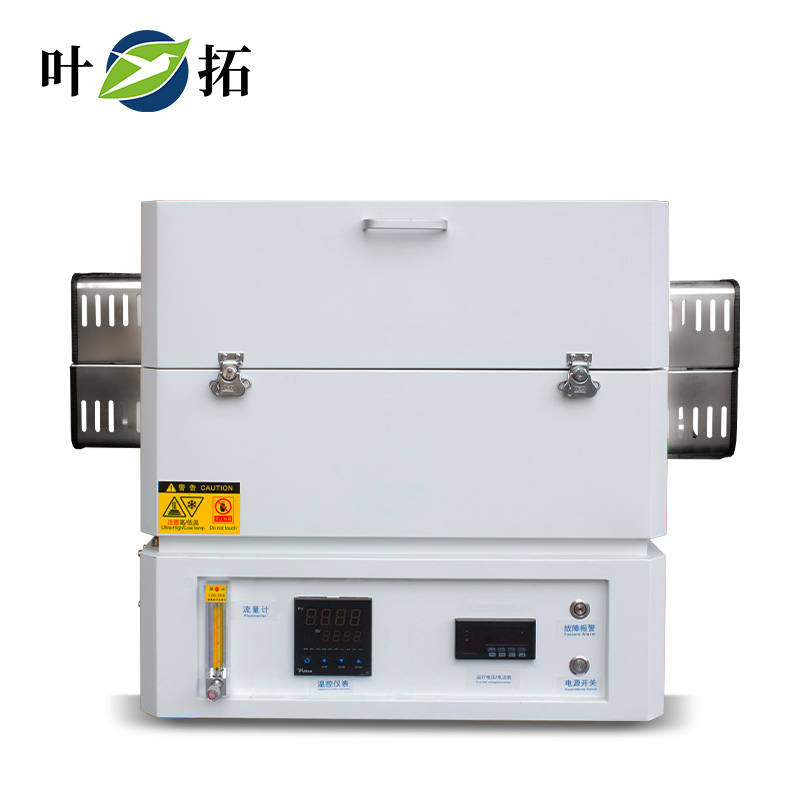
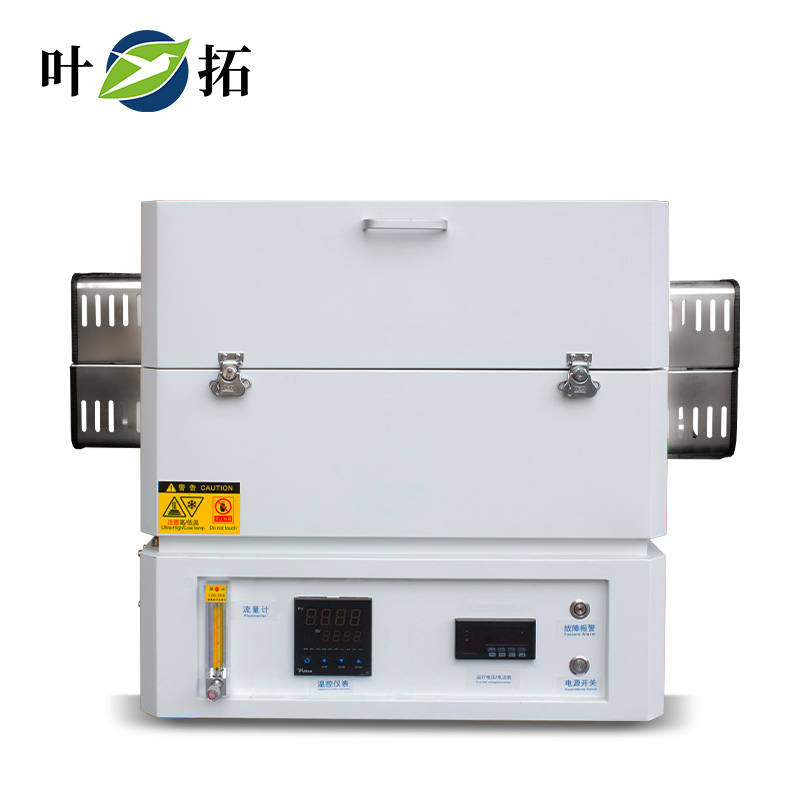
Product parameters:
Equipment model: YTGKD406-12
Temperature control range: room temperature -1200 ° C
Working temperature: ≤ 1100 ℃
Temperature control accuracy:<1000 ± 0.1 ℃; ≥ 1000±1°C
Constant temperature fluctuation: ± 1 ℃ (test point is 1000 ° C)
Temperature equilibrium: ± 3 ℃ (test point is 1000 ℃)
Heating rate: Recommended below 1000 degrees Celsius ≤ 10 ° C/min, with the fastest heating rate ≤ 30 ° C/min
Cooling rate: above 700 ° C ≤ 10 ° C/min
Furnace surface temperature: The surface temperature of the furnace body is less than room temperature+10 (measurement point is 1000 ° C)
External decoration: cold-rolled steel plate, surface resistance coating
Furnace body: ceramic fiber
Sensor: 1200 degree K-type thermocouple
Heating element: HDR high-quality resistance alloy wire
Cooling blade: axial fan
Furnace structure: double-layer shell structure, equipped with air cooling system
Control method: PID control
Setting representation: digital setting/digital display
Over temperature protection: integrated controller
Over temperature setting: Digital setting
Running function: Customized running/program running (30 segments of program temperature control)
Additional features: deviation correction, power outage compensation, lock key function
Timer: 1 minute -99 hours and 59 minutes, as well as 999 hours and 50 minutes. Digital setting, automatic operation, and fast automatic stop
Vacuum degree: Equipped with our company's high vacuum system, it can reach 1.33 * 10 to the 4th power pa (in an empty furnace state)
Insulation pipe blockage: 2 pieces, made of aluminum oxide material
Furnace tube: quartz tube
Vacuum column: heating area 400; Constant temperature heating area 200
Pressure gauge: -0.1 to 0.15mpa
Working environment: RT ± 5-40 ° C
Usage guarantee: door opening, power outage, over temperature alarm, leakage protection, over temperature protection
Furnace structure: horizontal
Furnace tube size: Φ 60mm
Power supply voltage: 220V50HZ
Input power: 4KW
- Product Details
- Product manual
Ye Tuo YTGKD406-12 Open Vacuum Tube Furnace
Model: YTGKD406-12
Product Overview:
Universities, research institutes, and industrial and mining enterprises conduct high-temperature sintering, metal annealing, and quality testing. Baking and pre sintering of zirconia discs in the powder metallurgy industry and denture processing industry. According to the size of the heating zone, conduct small-scale, pilot, and batch production
Product Features of Ye Tuo YTGKD406-12 Open Vacuum Tube Furnace
● External cold-rolled steel plate, surface resistance coating; Ceramic fiber furnace body, 1200 degree K-type thermocouple
Using HDR high-quality resistance alloy wire as the heating element
Adopting a double-layer shell structure, combined with thermal induction technology and equipped with an air cooling system, the surface temperature of the furnace body is rapidly cooled
Adopting KF quick flange reduces the possibility of heating tube damage, making material retrieval and placement more convenient and efficient
● Upward opening furnace cover design, real-time observation of heated materials, rapid cooling, meeting the needs of sudden cooling and heating
● Reserve quick interfaces for vacuum and gas circuits, to be used in conjunction with vacuum and mixing systems, to meet the needs of users for experiments under different vacuum conditions and atmospheric conditions
Equipped with safety operation functions such as door opening and power-off, over temperature alarm, and leakage protection. Additional deviation correction, power outage compensation, lock key function
Intelligent temperature control system with PID adjustment and self-tuning functions, and capable of programming 30 stages of temperature rise and fall
Equipped with 485 conversion interface inside the furnace, remote control, real-time tracking, historical recording, and output report
Advanced air insulation technology, combined with thermal induction technology, will automatically start the exhaust fan when the surface temperature of the furnace body reaches 50 ° C
50 segment programming, capable of connecting to computers. Complete remote control, real-time tracking, historical recording, and report output functions with single or multiple electric furnaces through a dedicated computer control system